Some Professional Suggestion on Assembling of Automotive Fasteners
Threaded fastener connections are one of the common joining methods in automotive applications, alongside welding, riveting, and adhesive bonding. The purpose of threaded fastener connections is to ensure intimate contact between joined components and withstand external forces. They offer advantages such as high precision, convenient assembly, and ease of disassembly.
Threaded connections are subjected to four types of external forces: tensile stress, shear stress, tensile + bending stress, and tensile + bending + shear stress. To ensure threaded fastener connections can withstand various static or dynamic external forces, the fastener must generate an axial clamping force on the joined components. This axial clamping force is provided by the applied torque. The bolt overcomes friction and undergoes elastic deformation according to the stiffness ratio between the bolt and joined components, forming clamping force between contact surfaces. Proper tightening processes should control this clamping force, making the essence of assembly tightening the precise control of the bolt's axial clamping force within an appropriate range.
During threaded fastener assembly, the dispersion of clamping force is influenced by the selected assembly method and external conditions. The clamping force must be sufficient to ensure reliable contact between components during operation without relative movement. Conversely, the applied clamping force must prevent bolt/component failure or plastic deformation during assembly and service. Market research indicates that most issues in bolted connections (e.g., loosening, fracture, component crushing) stem from imprecise or incorrect clamping force. Studies show that higher axial clamping force improves anti-loosening and fatigue performance, with optimal results achieved when bolts are tightened to yield point.
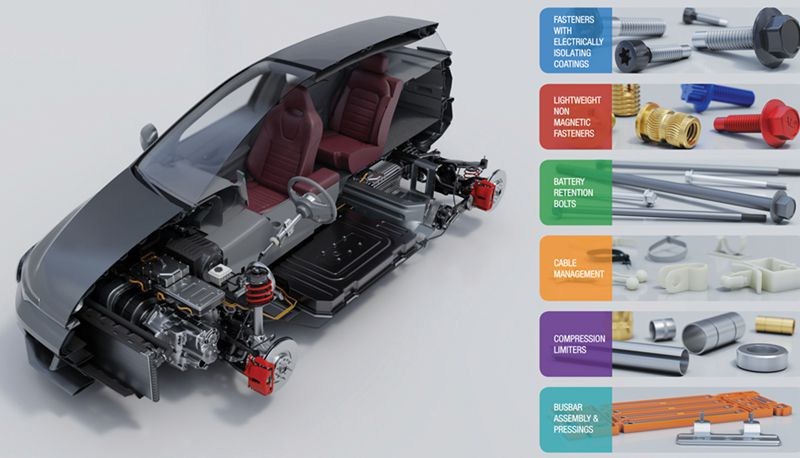
In automotive assembly lines, actual production cycle times and operations prevent direct measurement of clamping force for each bolted joint. Therefore, torque serves as an intermediate parameter for evaluating assembly quality. For torque control, tightening tool accuracy and tightening methodology are two critical factors. Generally:
Pneumatic tools: ±10%~40% torque accuracy
Manual torque wrenches: ~±10% accuracy
Electric screwdrivers: ±3%~5% accuracy
Tool selection and torque accuracy directly determine assembly grade.
China's automotive industry standard QC/T518-2013 ("Tightening Torque for Automotive Threaded Fasteners") classifies tightening accuracy into three grades (I, II, III), with corresponding torque tolerances and torque ratios shown in Table 1:
Table 1: Torque Ratios for Different Tightening Accuracy Grades
Grade Torque Scatter (±%) Torque Tolerance TM (N·m) Torque Ratio K₁
I 0.05 - 0.905
II 0.10 - 0.818
III 0.20 - 0.666
Note: K₁ = Min. Tightening Torque / Max. Tightening Torque
Taking a 10.9-grade M20×1.5×100 hex bolt with 0.12 friction coefficient as an example:
Grade III assembly yields lower target torque, larger torque fluctuation, and minimum clamping force.
Higher assembly grades increase target torque, reduce torque fluctuation, and enhance clamping force.
Grade I assembly increases target torque by 0.087% and improves clamping force by 32.5% compared to Grade III. According to international standards, when Grade III assembly requires M16 bolts, Grade I assembly can achieve equivalent performance with M12 bolts.
Implementing assembly grading for automotive threaded fasteners is essential. When receiving orders, fastener suppliers should prioritize technical agreement requirements. Compared to Grade III:
Grade I assembly increases target torque, reduces torque fluctuation, and enhances clamping force.
When maintaining identical clamping force requirements, Grade I enables smaller bolt sizes, achieving weight reduction, lightweight design, and more compact structures.
Peak Fasten Technologies are specialized in designing and manufacturing automotive fasteners and auto parts since establishment, kindly feel free to contact us for any query or bottleneck problems for threaded fasteners in this field.