The influence factor for the rust-resistant performance of Cr+3 Zinc Plating
The traditional zinc plating passivation uses hexavalent chromium passivation technology. This passivation film has the advantages of strong decorative appearance, good corrosion resistance, and self-repairing capabilities, hence its wide application. However, hexavalent chromium is a highly toxic substance that poses risks of carcinogenicity, teratogenicity, and inducing genetic mutations. It severely pollutes the environment and harms human health, leading to strict limitations on its use. Trivalent chromium's toxicity is about 1% of hexavalent chromium's, aligning with the trend of clean production.
Currently, employing trivalent chromium passivation has become a typical process for the surface treatment of fastener zinc plating. The primary concern is the corrosion resistance of the trivalent chromium passivation film, specifically its time to white rust and red rust appearance in neutral salt spray tests. The former depends mainly on the quality and sealing effect of the passivation film, while the latter relies on the thickness of the galvanized layer and the type of galvanizing process.
Zinc Plating, galvanize, environmental coating, surface treatment, surface finish, fasteners
1. Film formation mechanism of trivalent chromium passivation film:
The main components of the trivalent chromium passivation solution include trivalent chromium, oxidants, film-forming accelerators, complexing agents, and additives.
The primary film formation reactions of trivalent chromium passivation are as follows:
① Zinc dissolution process: Zn + Ox (oxidant) → Zn2+ + Ox -
Zn + 2H+ → Zn2+ + H2 ↑
② Film formation process: Zn2+ + xCr3+ + yH2O → ZnCrxOy + 2yH+
③ Film dissolution process: ZnCrxOy + 2yH+ → Zn2+ + xCr3+ + yH2O
2. Key characteristics of trivalent chromium passivation film:
The main features of trivalent chromium passivation film and hexavalent chromium passivation film are detailed in Table 1.
Items |
Cr+3 passivation film |
Cr+6 passivation film |
Regular Colors |
Blue White(Including White),Color,Black |
Blue White(Silver White), rainbow zinc,Green,Black. |
Composition |
100% trivalent chromium |
Trivalent chromium and hexavalent chromium coexist, with trivalent chromium being less soluble, stronger, contributing to the structural role, constituting approximately 30%; hexavalent chromium, more soluble and softer, acts on the galvanized layer for passivation purposes, constituting roughly 70%. |
Corrosion Resistance |
Due to the lack of self-repair capabilities, once the film layer is damaged, corrosion occurs rapidly. To enhance corrosion resistance in salt spray environments, it is necessary to "seal" the film. Compared to hexavalent chromium passivation films, the corrosion resistance of trivalent chromium color passivation films and trivalent chromium black passivation films is weaker. However, the corrosion resistance of trivalent chromium blue-white passivation films is similar to that of hexavalent chromium blue-white passivation films. |
The corrosion resistance is stronger, and even if the film layer is scratched, the passivation film's self-repair capability prevents a decline in its corrosion resistance. |
Heat resistance |
The heat resistance of trivalent chromium passivation film is superior to that of hexavalent chromium. Even at temperatures above 200℃ for an extended period, it retains more than 70% of its original corrosion resistance. This is particularly suitable for fasteners used under high-temperature conditions and for hydrogen-driven components like bolts of grade 10.9 and higher. |
Heating to above 80℃ for several minutes can easily dehydrate and crack the passivation film, exposing the galvanized layer, which results in decreased corrosion resistance. |
Microscopic morphology |
The surface cracks appear as regular oblique elongated patterns, fine and densely distributed. During the corrosion process, the passivation film lacks self-repair abilities; it only relies on these cracks to disperse corrosion currents, slowing down the corrosion rate to achieve corrosion resistance. |
The surface cracks form an irregular mesh pattern, and they are relatively larger in size. The presence of Cr6+ within these cracks grants the passivation film a certain degree of self-repair capability. |
3. Factors affecting the corrosion resistance of trivalent chromium passivation film
3.1 Influence Factors on Surface Protection Level Design
Average and Minimum Thickness of Zinc Plating Layer
The time for red rust to appear during neutral salt spray tests of zinc plating passivation films is directly related to the thickness of the zinc plating layer. To achieve good corrosion resistance, a minimum thickness of the zinc plating layer of at least 6μm is generally required. Additionally, a too-thin zinc layer can result in the dissolution of the plating during passivation.
Galvanizing Process and Brightening Agent
Currently, alkaline cyanide-free galvanizing and acid galvanizing are the two main zinc plating processes. Alkaline cyanide-free galvanizing is mainly used in appliances and communication equipment fasteners. Typically, the corrosion resistance of alkaline cyanide-free galvanizing is significantly better than that of acid galvanizing. Different galvanizing processes select different brightening agents, which can affect the formation process and intrinsic characteristics of the zinc plating layer, thereby impacting the film quality, adhesion, and corrosion resistance of the zinc plating passivation film.
Galvanizing Method
When the electroplating process, passivation process, and zinc plating layer thickness are the same, the corrosion resistance of hanging parts is significantly better than that of rolled parts. This is because rolled parts can only be electroplated at a lower current density (otherwise, the edges and corners of the plating are prone to burning), resulting in a thin plating in low current areas. Moreover, rolled parts are prone to collisions and scratches during passivation, which is one of the main reasons for the poor corrosion resistance of rolled parts.
3.2 Influential Factors in Production Site Management
Regular Analysis of Passivation Solution Components
During passivation, the zinc plating layer is dissolved and oxidized, causing the Zn2+ concentration in the passivation solution to continuously increase. When the Zn2+ concentration in the passivation solution is excessive, it affects the normal passivation process, affecting the control of passivation time and ultimately impacting the corrosion resistance of the zinc plating layer. Therefore, regular testing of Zn2+ and harmful impurity ion (such as Fe2+, Cu2+) concentrations is necessary to avoid passivation solution imbalances leading to issues such as poor appearance, fogging, and significantly decreased corrosion resistance of the passivation film, while also extending the life of the passivation solution.
Drying Temperature
The newly formed trivalent chromium passivation film after passivation is soft, has a high moisture content, and low strength. It must undergo proper drying at higher temperatures (i.e., "aging treatment"). Generally, the drying temperature is around 60-80°C. Excessive drying temperature or duration can lead to excessive dehydration of the passivation film, causing cracking and reducing the corrosion resistance of the zinc plating layer's passivation film in neutral salt spray corrosion tests. However, the drying temperature should not be too low, as insufficient aging can also decrease corrosion resistance.
Process Standardization
a. Pure water should be used to prepare trivalent chromium passivation solution because water quality directly affects the passivation film's performance.
b. When passivating rolled parts, it's best to use polypropylene material for the immersion hangers instead of stainless steel material. Due to the delicate nature of the passivation film, rolled parts should be rotated during drying, while hanging parts should be dried with cold air from an air gun before being dried, to avoid traces from dripping.
c. Trivalent chromium passivation should be performed by skilled operators, avoiding production habits from hexavalent chromium passivation. For instance, after passivating rolled parts, accelerating them immediately after being placed in a centrifugal dryer, or stacking and handling hanging parts without independent packaging after drying.
d. Regular maintenance of passivation tank equipment, frequent retrieval of workpieces that have fallen into the passivation tank, and cleaning of internal sludge to extend the passivation solution's life.
Component Collisions
Trivalent chromium passivation film should not experience collisions or scratches before and after drying, so it should be handled with care during transportation and handling.
3.3 Influence of Passivation Process Parameters
Volume Fraction of Passivation Agent
The volume fraction of the passivation agent is mostly between 10% to 20%. In production, it's essential to correctly control the proportion of the passivation agent, timely replenishing and adjusting it to ensure the corrosion resistance of the passivation film.
Passivation Time
The formation rate of the trivalent chromium passivation film is slow, requiring a longer immersion time. Typically, at room temperature, it takes over 45 seconds to obtain a high-protective passivation film. The passivation time is generally 60-90 seconds.
pH Value of the Passivation Agent
The pH value of the passivation agent directly affects the corrosion resistance of the passivation film. Therefore, periodic testing and adjustment of the pH value are necessary to ensure it stays within the optimal process range. The pH value is generally between 2.0 to 2.4.
Passivation Temperature
Low passivation temperatures result in slow formation of the passivation film, leading to a thin and less corrosion-resistant film. High passivation temperatures exacerbate the decomposition of surfactants and brighteners in the passivation solution, making film formation difficult, resulting in a loose passivation film structure and decreased corrosion resistance. Generally, passivation temperature ranges from 20 to 70°C, varying depending on the passivation system.
3.4 Factors Affecting Post-Passivation Sealing Processes
Types of Sealants
Sealing aims to improve the corrosion resistance (resistance to white rust and red rust), temperature resistance, and abrasion resistance of the passivation film, enhancing the product's appearance quality. Additionally, lubricants can be added to the sealant to adjust the surface friction coefficient of electroplated zinc passivation layers for vehicle fasteners. Different types of sealants yield different results in neutral salt spray tests.
Different Sealing Processes
There are two typical processes for trivalent chromium passivation: typical and simplified processes. The simplified process combines passivation and sealing into one step, simplifying the passivation process and improving production efficiency. Additionally, the passivation-sealing composite film formed by the simplified process can simultaneously meet requirements for appearance, mechanical properties, friction coefficient, and corrosion resistance. Therefore, compared to the typical process, the simplified process has significant advantages.
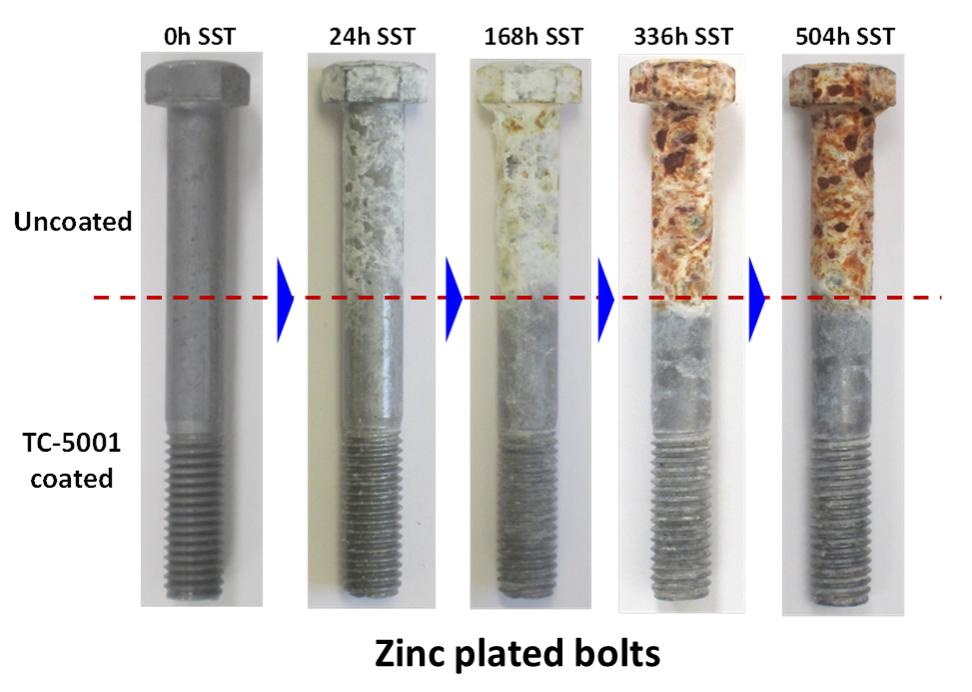
Appendix: Key Points for Quality Control of Electroplated Zinc Products
1. Ensure the composition content of the plating solution, conducting tests daily and replenishing timely. (Composition of plating solution: Chloride Potassium not less than 180-200g/L, Zinc Chloride not less than 40-45g/L, Boric Acid not less than 26-30g/L).
2. Ensure the area of the anode zinc plate and replace small zinc plates promptly.
3. Ensure normal operation of the tank's freezing equipment, controlling the tank temperature within 20-30°C.
4. Adjust the plating solution's pH value in time, adjusting with hydrochloric acid to between pH 5.8-6.4.
5. Properly prepare the blue-white zinc passivation solution by proportion (solution: nitric acid = 2:1), and measure the pH value hourly with test paper, adding appropriately (maintain pH: 2.0-2.5).
6. Timely replenish degreasing powder every shift.
7. Drain some old acid from the hydrochloric acid tank every day and replenish it with new acid.
8. Replace the new solution in the bright plating tank daily.
9. Treat iron impurities with hydrogen peroxide regularly, cleaning and replacing the filter core promptly.
10. Treat the plating tank solution with activated carbon regularly.
11. Set up a dedicated person to monitor the production line and grasp the product's quality status at any time. When leaving the tank, open it to check; unqualified products should not leave the tank. Identify the cause and handle it promptly.
12. Use a magnet to retrieve the blue-white zinc passivation tank once a day.
13. After drying the plated products, they must be dried on the drying road to prevent mold growth and maintain a bright appearance.
14. Check the thickness of products produced daily, ensuring that products subjected to salt spray tests are maintained at 5μm or more.
Peak Fasten Technologies is a professional custom fasteners supplier in China since 2010. We are dedicated into designing, producing and delivering high quality surface finish custom fasteners and metal parts to global market with professional engineers in all processes including design, structure, production processes, quality control etc. Please feel free to contact us if there is any query or bottleneck problems for parts coatings or corrosion issue in your industry.